9 estrategias eficaces para mejorar la retención de empleados en la industria manufacturera y reducir la rotación de personal
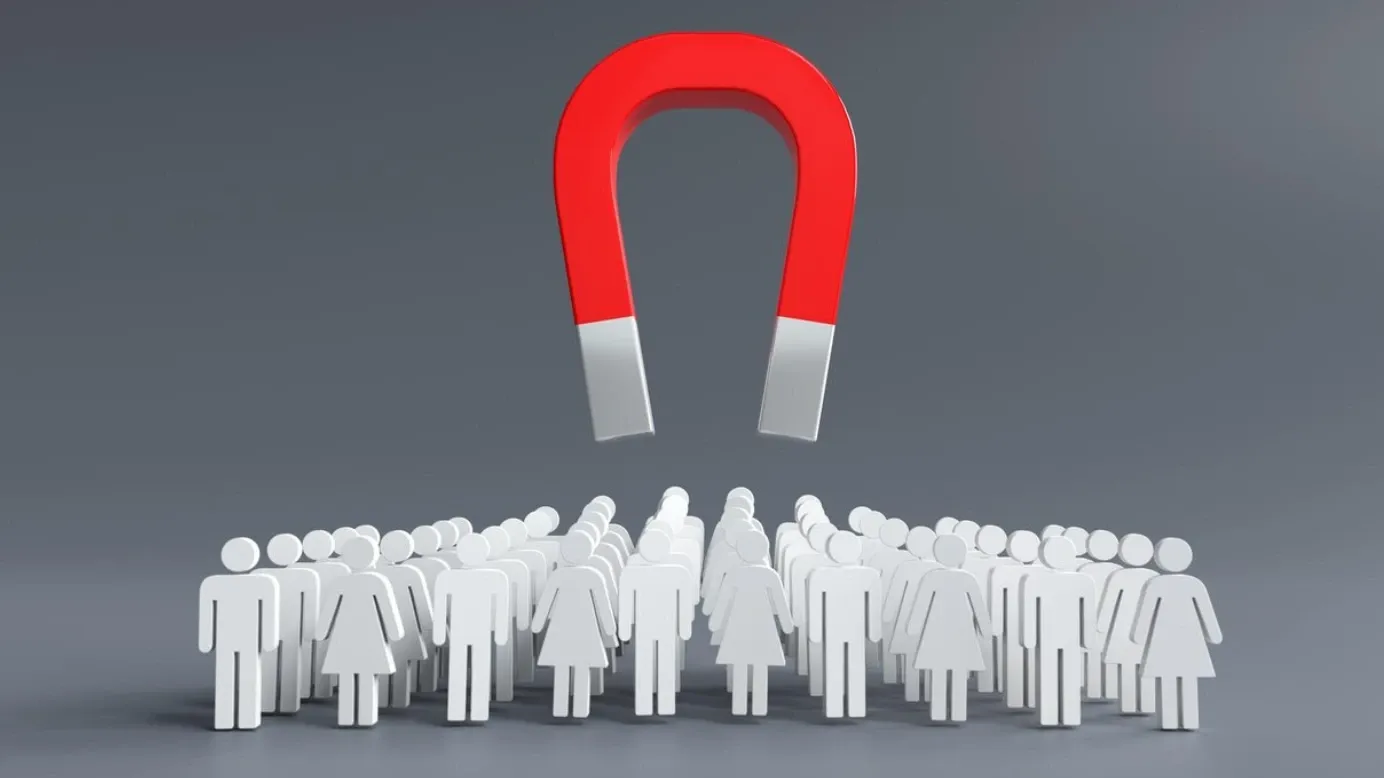
La retención de empleados en la industria manufacturera es un tema crítico e indica el desfase entre la demanda y la rotación de personal.
Aunque la demanda de los trabajadores ha ido en constante aumento desde la pandemia, en EE.UU. se ha observado una pauta de separación voluntaria del trabajo del 8,3%, con más de 63 millones de trabajadores que abandonan las empresas.
La rotación de personal en la industria manufacturera es cada vez mayor. Los estudios sugieren que la demanda de empleados es tan alta que más de 2,5 millones de puestos de trabajo hasta 2028.. Aunque hay una gran demanda de empleados y una baja tasa de desempleo del 4% en comparación con el 10% en 2010, la rotación en la industria ha sido alta y se atribuye a muchas razones.
En este blog, exploraremos por qué los empleados abandonan sus puestos de trabajo y qué estrategias pueden adoptar para reducir la rotación de personal y mejorar la retención.
Panorama de la mano de obra en el sector manufacturero
A escala mundial, la demanda de empleados no ha dejado de crecer en el sector manufacturero. Se necesitan empleados con talento y cualificados, con buena experiencia y una formación decente.
La industria manufacturera también ha sufrido un bache en los últimos tiempos, creciendo sólo marginalmente pero a un ritmo lento desde el cierre de la era Covid.
En mercado estadounidense ha registrado un en el empleo, con un aumento de la demanda pero una escasa tendencia a la contratación. Al aumentar la producción de las empresas de producción, aumenta la demanda de empleados cualificados, pero la oferta en el mercado es escasa.
Los empleados también cambian de trabajo y buscan pasivamente empleos mejores con mejores salarios, retribuciones y prestaciones generales, y un ambiente de trabajo positivo.
La tasa de desempleo en la industria manufacturera y de producción es del 3,2% en EE.UU., y hay más de 640.000 ofertas de empleo, cifra superior a la del año pasado. Esta tendencia al alza sugiere que, aunque hay demanda en el sector, las ofertas de empleo han ido en aumento, lo que denota la falta de retención de los empleados y la necesidad de mejorar la cultura y el entorno de trabajo, entre otros factores, para mejorar la retención de los empleados en las empresas.
Comprender la elevada tasa de rotación de personal en la industria manufacturera
La tasa de rotación de personal en la industria manufacturera es una de las más altas de todos los sectores, superando a menudo el 30% anual, y algunas empresas experimentan un desgaste aún mayor. Este ciclo constante de contratación y formación de nuevos empleados provoca pérdidas de productividad, un aumento de los costes operativos y una disminución de la moral en el lugar de trabajo.
Hay varios factores que contribuyen a la elevada rotación de personal en la industria manufacturera, como las escasas oportunidades de desarrollo profesional, los problemas de seguridad, las funciones repetitivas, la remuneración inadecuada y la falta de compromiso de los empleados. De hecho, muchos empleados abandonan la industria en busca de mejores salarios, mejores condiciones de trabajo o perspectivas de promoción profesional.
Para combatir este problema, las empresas deben aplicar estrategias eficaces de retención de empleados, como una remuneración competitiva, programas de desarrollo de habilidades, medidas de seguridad mejoradas y programas estructurados de recompensas y reconocimiento. Reducir la tasa de rotación de personal en la industria manufacturera no sólo mejora la estabilidad de la plantilla, sino que también aumenta la productividad general y el éxito empresarial.
Identificar los retos de la retención en la industria manufacturera
Los estudios y la investigación sugieren que hay muchas razones diferentes que afectan a la tasa de retención y a la tasa de abandono en las industrias manufactureras.
Cada empleado que abandona una organización le cuesta al empresario entre el 100 y el 150% de su salario para sustituirlo en puestos técnicos. En el caso de los empleados de mayor nivel salarial, puede costar entre una y dos veces el salario anual del empleado.
Una encuesta realizada en empresas del sector manufacturero reveló que los empleados con un buen nivel de compromiso y una cultura laboral positiva tenían "empleados comprometidos", con un 70 % más de productividad y un 70 % más de rotación de personal que el resto de los trabajadores no comprometidos.
Estos son los factores comunes que conducen a altos índices de rotación en la industria manufacturera:
1. Oportunidades de desarrollo profesional
A estudio sobre los empleados en 2019 reveló que la mayoría de los empleados se fueron por desarrollo profesional (un aumento del 17% con respecto a años anteriores). Esto se debe a cómo las empresas no ofrecen oportunidades de aprendizaje y desarrollo, ascensos y oportunidades de expansión profesional, todo lo cual puede ser aprovechado por la dirección para ayudar a los empleados.
2. Compromiso de los empleados
El compromiso de los empleados es una de las principales preocupaciones de los trabajadores en la era actual. Cuando los empleados están comprometidos, es menos probable que abandonen su puesto de trabajo. Según los estudios, el 52,6% de las empresas no tienen ningún tipo de compromiso por parte de los empleados. Los programas de recompensa y reconocimiento son una forma eficaz de fomentar el compromiso de los empleados en la industria manufacturera.
3. 3. Cultura de empresa
Un lugar de trabajo con una buena remuneración y una cultura laboral positiva, junto con programas de agradecimiento a los empleados, retiene a los empleados en un 93,5 por ciento durante 5 años de permanencia o más. Una buena cultura de empresa fomenta la positividad y la buena fe entre los empleados.
4. Compensación y beneficios deficientes para los empleados
La retribución y las prestaciones de los empleados son fundamentales para retenerlos en la industria manufacturera. Los salarios por hora de los empleados de producción y supervisión subieron un 5,5%. También se espera que los salarios suban un 3,9% adicional para ayudar a compensar mejor a los empleados.
5. Cuestiones de gestión y cuestiones con equipos/compañeros
Los empleados que tenían conflictos en el lugar de trabajo, microgestión por parte de jefes o directivos y celos o mala coordinación en el trabajo tenían un menor impulso y compromiso en el trabajo. El 29% de los empleados del sector manufacturero se enfrentan a conflictos de algún tipo en el lugar de trabajo, lo que provoca tensión y falta de compromiso.
Reducir la rotación en la fabricación con un mejor compromiso
Los empleados se van cuando no se sienten reconocidos y desconectados. Refuerce la retención con recompensas estructuradas, feedback continuo y una plantilla conectada mediante Empuls.
¿Cómo atraen empleados las industrias manufactureras?
He aquí cuatro formas eficaces de que las industrias manufactureras atraigan empleados.
1. Contratación de trabajadores diversos
La industria manufacturera es tristemente célebre por su falta de diversidad en la mano de obra. Un estudio de Deloitte arrojó luz sobre las diferencias de género en el sector manufacturero. Reflejaba que las mujeres tienen 1,8 veces más propensas a abandonar la industria. Y éste es sólo un aspecto de la diversidad. Había otras cuestiones sobre raza, edad, procedencia, etc. La industria ha sido testigo de cómo esta falta de diversidad ha provocado escasez de trabajadores cualificados.
Un análisis más detallado reveló que las empresas que practican la diversidad y fomentan entornos inclusivos tienen más probabilidades de obtener unos resultados financieros más sólidos. Por ejemplo, una empresa que ha incluido inmensamente la diversidad en su plantilla es The Hershey Company.
En palabras de Alicia Petross, Directora de Diversidad de Hershey's, "La diversidad es un elemento importante de la inclusión: queremos que la representación de nuestra plantilla refleje nuestra base de consumidores". Su programa de Diversidad, Igualdad e Inclusión (DEI) incluye aumentar la diversidad de su plantillaAumento del número de empleados negros (+7%), latinos (+13%) y asiáticos (+3%).
2. Construir percepciones positivas
Cambiar de perspectiva es una ardua responsabilidad. Muchos ni siquiera quieren considerar la fabricación como una opción profesional simplemente por su imagen de inflexibilidad o la falta de beneficios personales y monetarios. También luchan contra la imagen de ser un entorno inseguro y poco higiénico para trabajar.
Para superar este obstáculo, las empresas manufactureras se dirigen a los mercados locales y se comprometen a comunicación eficaz para mostrar las ventajas y beneficios de trabajar en la industria manufacturera. Los promocionan a través de portales de empleo y redes sociales para destacar las tecnologías avanzadas, la remuneración competitiva, la sólida cultura empresarial, la prioridad que dan a la seguridad y a las comunidades locales, etc.
Las empresas también se están centrando en los diversos conjuntos de habilidades necesarios para manejar la maquinaria, en lugar de en los trabajos físicamente exigentes. Demostrar que son un gran lugar ayuda mucho a crear una perspectiva positiva de la empresa y el entorno de trabajo.
3. Invertir en las recomendaciones de los empleados
La contratación nunca es un trabajo de una sola persona. Requiere la ayuda y la participación de distintos departamentos y de los empleados actuales. Lo mismo ocurre en la industria manufacturera, que depende enormemente de las recomendaciones de los empleados.
Antes de poner en marcha las remisiones, son cautos y sensibles sobre la ubicación y las ventajas que atraerían a los empleados. También les informan sobre las vacantes existentes y se aseguran de que el proceso de remisión sea fácil de entender.
Para fomentar la diversidad en la contratación, las empresas aprovechan los programas de recomendación de empleados para atraer a candidatos de distintos orígenes.
Por ejemplo, Glow forge, una empresa de fabricación de impresoras, ofrece 5000 dólares por cada persona contratada procedente de un entorno infrarrepresentado. La industria consigue dos objetivos con este plan. En primer lugar, pueden atraer a empleados diversos con un esfuerzo mínimo. En segundo lugar, también preparan y animan a los empleados actuales a trabajar con una mano de obra diversa.
4. Uso de la automatización
Las empresas manufactureras necesitan un gran volumen de trabajadores. Con tantos candidatos que contratar y poco personal para calificarlos a efectos de contratación, se hace necesario incluir cierta automatización en el proceso.
Para optimizar el proceso, las empresas utilizan sistemas de seguimiento de candidatos y robots. Ayudan a las empresas a llevar a cabo contrataciones de gran volumen, a encontrar talentos especializados y a cualificar a los candidatos en función de sus habilidades, formación y experiencia, acelerando así el proceso. De este modo, la empresa ahorra mucho tiempo y recursos que de otro modo gastaría en la contratación manual.
La automatización también agiliza la recopilación de datos, lo que ayuda a determinar el comportamiento y las expectativas de los candidatos. Además, atrae a las nuevas generaciones para que se inscriban en una fábrica inteligente equipada con tecnología punta y que abraza la digitalización.
Estrategias de retención de empleados en la industria manufacturera
Los altos índices de rotación de personal pueden afectar significativamente a la retención de empleados en la industria manufacturera, provocando un aumento de los costes de contratación, una disminución de la productividad y trastornos operativos. La aplicación de estrategias de retención sólidas puede ayudar a las empresas a crear una plantilla más comprometida y motivada. He aquí nueve ideas para retener a los empleados en la industria manufacturera:
1. Ofrecer oportunidades de crecimiento
La industria manufacturera vuelve a tener la imagen de falta de crecimiento. Y es comprensible, porque es difícil comprometerse cuando se realizan diariamente las mismas tareas repetitivas. Para solucionarlo, las empresas manufactureras tienen que averiguar cuáles son sus expectativas y trabajar para conseguirlas a través de la formación y la experiencia. Esto ayudará a los empleados a comprometerse desde el primer día y, a largo plazo, fomentará la lealtad, especialmente entre la mano de obra más joven.
Fomentar retención de empleados entre los trabajadores fijos, las empresas invierten en desarrollar sus habilidades porque saben que eso mantendrá el barco a flote. Demuestra que las empresas se preocupan por la carrera profesional de sus empleados y quieren que acaben ascendiendo en la empresa.
La mejor forma de hacerlo es definiendo una trayectoria profesional clara para todos los empleados desde el momento en que empiezan a trabajar. Utilizan software de gestión de competencias, ofrecen oportunidades de desarrollo profesional e incluso animan a los directivos a informarse sobre los objetivos a largo plazo de sus equipos.
2. Definir las expectativas desde el principio
La investigación demuestran que el incumplimiento de los compromisos es una de las principales razones para dejar de fumar. Por eso es necesario fijar objetivos y expectativas realistas desde el principio. Las empresas están tomando nota de esto, ya que las promesas incumplidas arruinan la confianza de los empleados en la empresa. En su lugar, están siendo más transparentes sobre las oportunidades de trabajo y la cultura de la empresa.
Disponga de un sólido proceso de incorporación en el que los empleados conozcan en detalle cómo funciona la empresa, quiénes son los miembros de su equipo, cuáles son las políticas de la empresa, el equilibrio entre la vida laboral y personal, las precauciones de seguridad, etc. Cuanto más exacto sea el proceso de incorporación, más realistas serán las expectativas que se establezcan.
3. Reevaluar el entorno de trabajo de la empresa
Crear un entorno libre de peligros y más bien apto para el trabajo para los empleados en la fabricación no es mucho pedir. Resulta tanto más importante cuanto que los ruidos fuertes, las temperaturas no convencionales, los materiales polvorientos o aceitosos y otras condiciones pueden llegar a ser frustrantes rápidamente.
En estos casos, las empresas toman precauciones adicionales para disponer de salas de descanso más limpias y grandes, y añaden ventiladores o calefactores para que el aire circule adecuadamente y los empleados puedan tomarse un respiro. Del mismo modo, si en una planta de fabricación no se ofrecen las condiciones necesarias para trabajar y sobrevivir a diario, es probable que los empleados se marchen y no vuelvan a mirar atrás.
Las empresas también reevalúan la cultura si es necesario. Por ejemplo, ¿animan a los empleados a tomarse descansos? ¿Ofrecen obsequios de vez en cuando? ¿Ofrecen viajes o seguros? Si las empresas ofrecen todas las ventajas y demuestran que se preocupan por sus empleados, éstos se lo pensarán mucho antes de marcharse.
4. Encontrar motivos para dejar de fumar
Para retener, primero hay que saber por qué los empleados renuncian en primer lugar. Para ello, las empresas buscan desarrollar estrategias de retención dentro de sus empresas en lugar de seguir una ruta genérica de otros sectores para retener a los empleados. La mejor manera de hacerlo es preguntando directamente a sus empleados.
Las empresas están utilizando las encuestas de salida como la forma más común y eficaz de recabar la opinión de los empleados en relación con la rotación. Otros métodos comunes son las encuestas anuales de satisfacción, las entrevistas de salida y los estudios de permanencia. Independientemente de lo que utilice finalmente, estos métodos le proporcionarán información basada en datos sobre los motivos por los que los empleados quieren irse o incluso quedarse.
5. Compromiso y reconocimiento de los empleados
Los empleados que se sienten comprometidos en su lugar de trabajo tienen una calidad de vida muy alta y rinden más en el trabajo que los que no se sienten comprometidos. Las empresas que se esfuerzan activamente por recompensar y reconocer a sus empleados tienen trabajadores comprometidos, mientras que las que no lo hacen pueden tener "abandonos totales", lo que constituye un grave problema en la industria cervecera.
La industria manufacturera actual se denomina ' La gran resignación en la que cada vez más personas cambian de trabajo y dejan a sus empleadores por otros mejores. Millones de personas han abandonado su trabajo desde principios de 2021 en busca de empleos que merezcan la pena. Algunas estrategias que deberían adoptar las empresas manufactureras son:
- Tener una gran cultura de trabajo
- Cultura de crecimiento positivo
- Diversidad e inclusión
- Una retribución equilibrada
- Programas de recompensa y reconocimiento
- Muchas ventajas y beneficios, etc,
Todos estos son algunos consejos que deben idearse con cuidado y eficacia para garantizar la retención de los empleados.
- Los empresarios deben ser capaces de celebrar el éxito de los empleados y señalar sus logros e hitos importantes para que se sientan especiales y valorados.
- Las contribuciones de los empleados no deben pasarse por alto y debe llevarse a cabo un reconocimiento tanto formal como informal.
- Las recompensas pequeñas y grandes en forma de comisiones e incentivos, bonificaciones, recompensas en metálico, tarjetas regalo, muestras de agradecimiento, certificados de honor e insignias deben incorporarse de alguna manera.
Un ejemplo de un gran sistema de recompensa y reconocimiento que se está utilizando en una empresa manufacturera es el de Trussway - una empresa manufacturera que utilizó un programa de recompensas para empleados que refleja el bienestar de los empleados.
La empresa ofrece un plan que ayuda a los empleados valiosos a gestionar su jubilación poniendo en marcha un sistema de transición para retrasar las jubilaciones, un esfuerzo por retener a los empleados cualificados.
Su concurso de sugerencias e ideas convoca grandes ideas de los empleados con un premio en metálico de 1.000 USD a 2.500 USD para los ganadores. Además, la seguridad de los empleados es lo primero, lo que contribuye a reducir la rotación.
Recompense a su equipo de fabricación de la forma adecuada
El reconocimiento no es sólo una gratificación, es la clave para mantener a los empleados comprometidos. Demuestre su aprecio con recompensas por hitos, reconocimiento entre compañeros e incentivos basados en el rendimiento adaptados a la industria manufacturera.
6. Compensación y prestaciones competitivas
A estudio realizado por el instituto de fabricación en colaboración con Colonial life revela que encontrar la mano de obra cualificada adecuada ha sido un reto durante mucho tiempo e incluso con una elevada demanda en el mercado, el 93% de los puestos de las empresas quedarán sin cubrir debido a la competencia en el espacio de fabricación.
El 83% de las empresas de este grupo han aumentado su retribución para seguir siendo relevantes y competitivas en el mercado, incluyendo beneficios para los empleados, salarios más altos ventajas e incentivos para atraer mano de obra cualificada.
Es difícil encontrar el equilibrio adecuado entre una estructura retributiva que se ajuste al presupuesto de la empresa, mejore la satisfacción en el trabajo y cumpla las normas y expectativas de los empleados.
Si se establece una buena estructura de remuneración y se comunican claramente los beneficios monetarios y no monetarios de trabajar con una determinada planta de fabricación, se puede mejorar drásticamente la retención de los empleados.
Algunas estrategias de las que pueden valerse las empresas manufactureras para ofrecer una buena retribución y prestaciones que retengan a los empleados son:
- Una estructura retributiva completa
Los salarios estándar del sector y un pequeño extra pueden ayudar mucho a demostrar cuánto se valora a los empleados. Proporcione también jubilación, fondo de pensiones y otros beneficios monetarios asociados a los salarios para obtener una remuneración completa.
- Ofrecer diversas ventajas y flexibilidad
Las prestaciones de los seguros son cada vez más sofisticadas, por lo que hay que elegir planes atractivos que cubran aspectos del empleado como la salud, la odontología, la oftalmología, las prestaciones por accidente, la asistencia familiar y los programas de asistencia al empleado.
- Beneficios monetarios y no monetarios
No todos los empleados consideran que los beneficios monetarios sean los únicos dignos de tener en cuenta: hay un montón de beneficios no monetarios que facilitan la vida de los empleados en el sector manufacturero, como los días libres pagados, las vacaciones pagadas, la oportunidad de recibir formación adicional y programas certificados, los turnos y horarios de trabajo flexibles, los programas de recompensas, etc., que pueden ser una excelente forma de compensar a los empleados.
Uno de los mejores estudios de casos de una empresa que tiene un sistema de compensación y beneficios bien establecido y que ha retenido a los empleados de fabricación gracias a él es Denso - una empresa de fabricación de piezas para automóviles.
La empresa ha ideado atractivos paquetes retributivos que se centran más en retener a los empleados que en atraer a otros nuevos.
Han establecido un turno de 20 horas semanales para ofrecer un horario flexible, que es lo más popular entre los empleados. También tienen otras ventajas, como transporte gratuito para los empleados, comidas gratuitas, guarderías, ayudas a la educación para el desarrollo profesional, etc.
7. Formación y desarrollo de competencias
La formación y el desarrollo están estrechamente relacionados con los índices de rotación y desgaste de los empleados en las organizaciones.
Dado que el desarrollo profesional y la falta de formación son la razón número 1 por la que los empleados abandonan su puesto de trabajo, ofrecer oportunidades para mejorar sus competencias, continuar su formación e invertir en oportunidades de crecimiento para los empleados se ha convertido en algo primordial. En un estudio se reveló que el 74% de los empleados estaría dispuesto a reciclarse para seguir siendo empleables y relevantes en el sector.
En el sector manufacturero, los empleados esperan recibir una formación continua que les ayude en su trabajo y en el desarrollo de su carrera profesional y que les acerque a sus objetivos en la vida.
Muchas empresas del mundo, y especialmente de EE.UU., ofrecen oportunidades de crecimiento invirtiendo en sus empleados:
- Oportunidades educativas
- Programas certificados
- Talleres de formación
- Cursos en línea
- Finalización de estudios y formación continua, etc.
También se espera de las empresas que ofrezcan una trayectoria profesional clara y celebren reuniones de consecución de objetivos profesionales que ayuden a establecer en qué punto se encuentra el empleado en sus objetivos profesionales.
Muchas empresas y sus equipos de RR.HH. celebran una reunión de consecución de objetivos a los 90 días de incorporarse y anualmente para ayudar a los empleados a saber dónde están y dónde pueden llegar.
Un buen ejemplo de empresa que utiliza este enfoque es Ketchie - una empresa de fabricación de ingeniería de precisión. La empresa ofrece semanas laborales de cuatro días y una serie de beneficios a los empleados para retenerlos, uno de los cuales es el sistema de retroalimentación centrado en los objetivos de los empleados.
8. Seguridad y entorno laboral
Un enfoque de "la seguridad ante todo" hacia los empleados demuestra que éstos los valoran y se preocupan por su bienestar. En un estudio, se descubrió que los empleados de la industria manufacturera tenían 300 accidentes mortales al año y más de 400.000 lesiones no mortales. de media.
La seguridad en el lugar de trabajo también está vinculada a los requisitos de cumplimiento y auditoría de la fábrica y, por tanto, las instalaciones de fabricación deben asegurarse de que se cumplen estas directrices para mantener a salvo a los empleados y retenerlos mejor.
Los lugares de trabajo pueden presentar múltiples peligros que, si no se tienen en cuenta, pueden provocar daños y lesiones graves. Algunos ejemplos de la responsabilidad del empresario respecto a la seguridad de los trabajadores son:
- Todas las zonas expuestas al agua, al fuego y a caídas o lesiones deben estar claramente señalizadas.
- Los empleados deben recibir equipos de protección, mascarillas y kits de EPI cuando proceda en función del tipo de instalación.
- Los empleados deben recibir atención médica, acceso a primeros auxilios y un seguro médico que les ayude en caso de emergencia médica.
- Las grandes instalaciones también deben contar con un equipo médico interno.
- Deben realizarse auditorías periódicas para garantizar el cumplimiento de la legislación laboral.
La seguridad en el trabajo es un parámetro clave para retener a los empleados. El 75% de los empleados en EE.UU. han declarado que su lugar de trabajo no tenía el nivel esperado de medidas de seguridad para los empleados. El 81% de los empleados cree que su seguridad física es de suma importancia a la hora de elegir un lugar de trabajo.
Esto significa que los empleados que eligen una empresa y permanecen en ella necesitan saber que es segura para ellos. Incluir la atención médica y el seguro médico en la indemnización es solo arañar la superficie de lo que los empleados esperan de las empresas.
- Garantizar un lugar de trabajo seguro y saludable
- Abordar los riesgos y problemas en el lugar de trabajo
- La correlación entre seguridad y retención de empleados
9. Estrategias de retención basadas en datos
Los empleadores pueden utilizar datos fiables y predictivos para comprobar los índices de rotación y retención de empleados, de modo que las empresas puedan identificar las áreas en las que necesitan trabajar sobre los posibles factores de riesgo que les están provocando la rotación.
Perder empleados formados y cualificados puede costar entre el 13% y el 23% de la remuneración anual además de otros factores de riesgo, como la pérdida de partes interesadas, cuentas con las que trataban y clientes a los que atendían.
Mediante el uso de estrategias basadas en datos y modelos predictivos, los equipos de RRHH pueden analizar las causas por las que los empleados se marchan e idear programas de mitigación de riesgos. Algunos datos y estrategias del enfoque de retención basado en datos son:
Muchas grandes empresas utilizan ahora diversos programas y herramientas para registrar el comportamiento de los empleados, su estado de ánimo, sus niveles de compromiso, sus niveles de estrés, su carga de trabajo, sus relaciones con los compañeros, etc., con el fin de analizar su tendencia a la retención.
Organizaciones de recopilación de datos e investigación como Gartner han ayudado a las empresas a recopilar datos de las formas menos convencionales para analizar el comportamiento de los empleados y la rotación de personal en el sector manufacturero.
El uso de entrevistas de salida es fundamental para comprender las causas de la marcha de los empleados y utilizar los comentarios y datos para ayudar a crear estrategias de retención mejores y más eficaces.
Utilizar el modelo de selección adecuado, como la contratación basada en datos, ayuda a retener a los empleados, ya que la mayoría de las personas renuncian porque consideran que su trabajo no se ajusta a sus objetivos a largo plazo.
Las investigaciones de Glassdoor sugieren que la mayoría de la gente empieza a buscar trabajo en enero, lo que puede ayudar a los empresarios a prestar especial atención a los empleados para ayudar a mitigar el riesgo de desgaste.
El uso de entrevistas de permanencia y una prima de retención/permanencia asociada y un método regular de encuesta de compromiso de los empleados puede ayudar a aumentar la retención de los empleados.
Un ejemplo de empresa que utiliza el análisis predictivo para retener a sus empleados es Continental, un fabricante de piezas para automóviles. La fábrica de la empresa en México tenía una rotación de personal muy elevada, lo que obligó a utilizar análisis predictivos y modelos basados en datos para saber cómo contratar a los empleados adecuados, predecir la rotación de personal y mitigar el riesgo mediante diversas estrategias, como planes de acción, encuestas, seguimientos, diversidad e inclusión, etc.
Ejemplos de empresas de la industria manufacturera que están haciendo un excelente trabajo para atraer y comprometer a sus empleados
Estos son algunos ejemplos de empresas de la industria manufacturera que están haciendo un trabajo impresionante a la hora de atraer y comprometer a sus empleados.
1. NVIDIA
Nvidia es conocida en el sector de las unidades de procesamiento gráfico y los chips informáticos. La empresa se considera un referente en el fomento del compromiso de los empleados en el sector manufacturero.
Organiza periódicamente actividades como actividades de divulgación comunitaria y de creación de equipos para promover mejores relaciones laborales y eliminar la competencia malsana. También fomenta un entorno productivo para que los trabajadores puedan perfeccionar sus habilidades creativas con la autonomía adecuada.
2. Stryker
Esta empresa líder en tecnología médica es conocida por atraer a empleados existentes para nuevas funciones y ofrecer oportunidades en investigación y desarrollo, gestión de productos y control de calidad. También ofrece a sus empleados increíbles prestaciones, como una amplia cobertura sanitaria, ayudas para la matrícula y un plan de ahorro para la jubilación.
3. Manzana
Apple ha creado una cultura orientada a la innovación en la que ha transformado sus unidades para mejorar su capital humano y promover el desarrollo de los equipos. Fomenta el compromiso convirtiendo a los empleados en sus mayores embajadores de marca y ofreciéndoles ventajas y descuentos en los productos. También ofrece acciones gratuitas y subvenciones para animarles y potenciar su creatividad en el trabajo.
4. 4. General Electric
General Electric ha introducido muchos cambios en sus procesos de contratación y se ha centrado en crear una estrategia de contratación equilibrada que anime a más mujeres a presentar su candidatura.
En uno de sus vídeos promocionales, anunció el objetivo de GE de emplear a más de 20.000 mujeres en puestos técnicos para 2020. También hace mucho hincapié en el compromiso y el desarrollo de los empleados reembolsándoles los gastos de matrícula y ofreciéndoles una amplia formación para que crezcan en su carrera profesional.
5. L'oreal
L'oreal ha creado una propuesta de valor para sus empleados con el fin de atraer a otros nuevos. La propuesta de valor para los empleados incluye los valores y la cultura que la empresa encarna y ofrece a sus empleados.
Los empleados actuales concluyeron que L'oreal es una empresa inspiradora, una escuela de excelencia y que trabajar allí es una experiencia apasionante. ¿El resultado? Casi el 70% de sus seguidores en LinkedIn quieren solicitar trabajo en la empresa.
Retenga a sus empleados y reduzca la rotación con Empuls
La elevada rotación de personal es un reto constante en la industria manufacturera. Los turnos largos, el trabajo físicamente exigente y la falta de reconocimiento suelen hacer que los empleados se sientan infravalorados y desconectados. Sustituir a los trabajadores cualificados es costoso, pero el verdadero reto consiste en mantenerlos implicados, motivados y comprometidos con su organización.
Empuls ofrece soluciones de compromiso de los empleados para la industria manufacturera que van más allá de los cheques de pago, creando un lugar de trabajo donde los empleados se sienten apreciados, escuchados e involucrados en el éxito de la empresa.
Cómo ayuda Empuls a retener a los empleados del sector manufacturero:
- Reconozca y premie la lealtad: Celebre los aniversarios laborales, los logros en seguridad y las contribuciones destacadas con recompensas e incentivos significativos.
- Dé voz a los empleados: Realice encuestas de opinión en tiempo real para conocer las preocupaciones, abordar los retos y fomentar una cultura de mejora continua.
- Refuerce la conexión en el lugar de trabajo: Mantenga el compromiso de los trabajadores de primera línea y de fábrica mediante una intranet social que fomente la comunicación y el trabajo en equipo.
- Proporcione ventajas y beneficios significativos: Ofrezca beneficios complementarios libres de impuestos, recompensas por hitos e incentivos que añadan un valor real a la vida de los empleados.
- Aumentar la satisfacción y la motivación en el trabajo: Cree un entorno en el que los empleados se sientan respetados, apoyados y motivados para quedarse a largo plazo.
Retener no consiste sólo en cubrir puestos, sino en crear un entorno en el que los empleados quieran quedarse. Con Empulslas empresas manufactureras pueden construir una cultura de trabajo que priorice el reconocimiento, el compromiso y la implicación a largo plazo. Conecte ahora con nuestros expertos en compromiso de los empleados¡!
Reflexiones finales
Como en la mayoría de las industrias, los empleados son también el mayor activo de la industria manufacturera. Pero la mano de obra actual tiene muchas opciones a su disposición. Tienen acceso a recursos y contactos que pueden ayudarles a conseguir un buen empleo en cualquier otro campo.
En consecuencia, las empresas manufactureras están haciendo esfuerzos especiales para atraer y retener a estos empleados, ya que los entornos de trabajo en el sector manufacturero suelen dar lugar a altas tasas de rotación, lo que puede servir de ejemplo.