9 Effective Strategies for Improving Employee Retention in the Manufacturing Industry & Reducing Turnover
High turnover is a major challenge in manufacturing. Implementing effective employee retention in manufacturing industry can help businesses enhance job satisfaction, improve productivity, and build a committed workforce.
On this page
- The manufacturing workforce landscape
- Understanding the high turnover rate in the manufacturing industry
- Identifying retention challenges in the manufacturing industry
- How are manufacturing industries attracting employees?
- Employee retention strategies in manufacturing industries
- Examples of companies in the manufacturing industry that are doing an awesome job in attracting & engaging employees
- Retain your manufacturing workforce & reduce turnover with Empuls
- Finishing thoughts
Employee retention in the manufacturing industry is a critical subject and indicates the gap between employee demand and employee turnover.
Although employee demand has been on a steady rise since the pandemic, the US has seen a pattern of voluntary separation from work at 8.3 percent, with over 63 million workers leaving companies.
Employee turnover in the manufacturing industry is at an ever-high. Studies suggest that employee demand is so high that more than 2.5 million jobs may not be filled until 2028. Even though there is a high demand for employees and a low unemployment rate of 4 percent when compared to 10 percent in 2010, the turnover in the industry has been high and is attributed to many reasons.
In this blog, we will explore why employees leave their jobs and what strategies employees can adopt to reduce employee turnover and improve retention.
The manufacturing workforce landscape
On the global front, employee demand has been steadily growing on the manufacturing front. There is a need for talented and skilled employees with good experience and decent educational backgrounds.
The manufacturing industry has also faced a slump in recent times, only growing marginally but at a slow pace since the closure of the Covid era.
The US market has seen a sudden drop in employment, with rising demand but a poor hiring trend. With output from production companies increasing, there is a rise in demand for skilled employees but poor supply in the market.
Employees are also moving jobs and passively looking for better jobs with better pay, overall compensation and benefits, and a positive work atmosphere.
The unemployment rate in the manufacturing and production industry is at 3.2 percent in the US, and there are more than 640,000 job openings, which is higher than last year. This upward trend suggests that even though there is a demand in the industry, the job openings have been rising which denotes the lack of employee retention and a scope for improving work culture, environment, and other factors to improve employee retention within companies.
Understanding the high turnover rate in the manufacturing industry
The manufacturing industry turnover rate is one of the highest across all sectors, often exceeding 30% annually, with some companies experiencing even higher attrition. This constant cycle of hiring and training new employees leads to productivity losses, increased operational costs, and reduced workplace morale.
Several factors contribute to high turnover in manufacturing, including limited career growth opportunities, safety concerns, repetitive job roles, inadequate compensation, and lack of employee engagement. In fact, many employees leave manufacturing jobs in search of better pay, improved working conditions, or career advancement prospects.
To combat this issue, companies must implement effective employee retention strategies, such as competitive compensation, skill development programs, improved safety measures, and structured rewards and recognition programs. Lowering the manufacturing industry turnover rate not only improves workforce stability but also enhances overall productivity and business success.
Identifying retention challenges in the manufacturing industry
Studies and research suggest that there are many different reasons that affect the retention rate and the attrition rate in the manufacturing industries.
Each employee that leaves an organization costs an employer around 100 to 150 percent of an employee's salary to replace the same employee regarding technical jobs. For employees at a higher pay grade, it can cost one to two times an employee's annual salary.
A survey of the manufacturing sector companies found that employees with good employee engagement and positive work culture had ‘engaged employees’ with 70 percent better productivity and 70 percent better turnover than the rest of the disengaged workers.
Here are the common factors that lead to high turnover rates in the manufacturing industry:
1. Career development opportunities
A study on employees in 2019 revealed that most employees left for career development (a 17 percent increase from previous years). This is because how companies do not provide learning and development opportunities, promotions, and career expansion opportunities, all of which can be taken up by the management to help employees.
2. Employee engagement
Employee engagement is one of the top concerns for employees in today’s era. When employees are engaged, they are less likely to leave their workplace. It was found in studies that 52.6 percent of companies had no employee engagement at all. Rewards and recognition programs are an effective way to promote healthy employee engagement in the manufacturing industry.
3. Company culture
A workplace with good compensation and positive work culture, along with programs for employee appreciation, retains employees by 93.5 percent for 5 years tenure or more. A good company culture promotes positivity and good faith among employees.
4. Poor employee compensation and benefits
Employee compensation and benefits are key to employee retention in the manufacturing industry. Hourly wages of production and supervisory employees rose by 5.5 percent. The wages are also expected to rise by an additional 3.9 percent to help compensate employees better.
5. Manager issues and issues with teams/ peers
Employees who had conflicts in the workplace, micromanagement from employers or managers and jealousy or poor coordination at work had a reduced drive and engagement at work. 29 percent of employees in the manufacturing sector faced conflicts of some or other type within the workplace, which causes tension and disengagement.
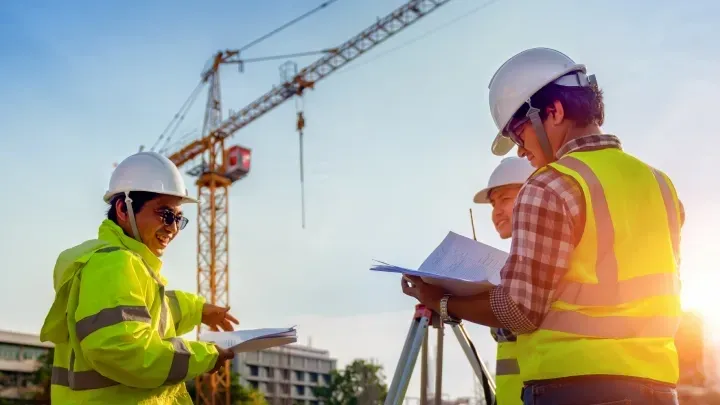
Reduce Manufacturing Turnover with Better Engagement
Employees leave when they feel unrecognized and disconnected. Strengthen retention with structured rewards, continuous feedback, and a connected workforce using Empuls.
How are manufacturing industries attracting employees?
Here are four effective ways in which manufacturing industries can attract employees.
1. Hiring diverse workers
The manufacturing industry was infamous for its lack of diversity in the workforce. A study by Deloitte shed light on the gender differences in the manufacturing sector. It reflected that women are 1.8 times more likely to leave the industry. And this is just one aspect of diversity. There were other issues about race, age, background, etc. The industry has witnessed how this lack of diversity has led to shortages of skilled workers.
Further analysis revealed that companies practicing diversity and encouraging inclusive environments are more likely to have a stronger financial performance. For example, one company that has immensely included diversity in its workforce is The Hershey Company.
In the words of Alicia Petross, Chief Diversity Officer at Hershey's, “Diversity is an important element in inclusion — we want our workforce representation to mirror our consumer base.” Its Diversity, Equity, and Inclusion (DEI) agenda includes increasing its workforce diversity: gains across Black (+7%), Latinx (+13%), and Asian (+3%) workforce segments.
2. Building positive perceptions
Changing a perspective is a hard responsibility. Many don’t even want to consider manufacturing as a career option simply because of its image of being inflexible or the lack of personal and monetary benefits. They also struggle with the image of being an unsafe and unhygienic environment to work in.
To overcome this barrier, manufacturing companies are targeting the local markets and engaging in effective communication to show the benefits and perks of working in manufacturing. They’re marketing them via career sites and social media to highlight the advanced technologies, competitive compensation, strong company culture, and how they’re putting safety and local communities first, etc.
Companies are also focusing on the diverse skill sets required to operate machinery rather than the physically demanding jobs. Showing that they’re a great place helps a lot in building a positive outlook for the company and the working environment.
3. Investing in employee referrals
Recruitment is never a one-person job. It requires assistance and participation from different departments and current employees. The same applies to the manufacturing industry, which relies immensely on employee referrals.
Before implementing referrals, they’re cautious and sensitive about the location and the perks that would attract the employees. They’re also educating them on the existing vacancies and ensuring the referral process is easy to understand.
To encourage diversity in hiring, companies are leveraging employee referral programs to attract candidates from different backgrounds.
For example, Glow forge, a printer manufacturing company, offers $5000 for every referral hired from an underrepresented background. The industry achieves two objectives via this scheme. First, they can attract diverse employees with minimal effort. Secondly, they also prepare and encourage the existing employees to work with a diverse workforce.
4. Using automation
Manufacturing companies require a high volume of workers. With so many candidates to hire and few staff to qualify them for hiring purposes, it becomes necessary to include some automation in the process.
To optimize the process, companies are leveraging applicant tracking systems and bots. They help the companies support high-volume recruitment, source niche talent, and qualify the candidates based on their skill sets, backgrounds, and experience eventually hastening the process. It saves ample time and resources for the company that it otherwise spends on manual hiring.
Automation also streamlines data collection, which helps determine candidate behavior and expectations. It also attracts the new generation to enroll in a smart factory that is equipped with state-of-art technology and embraces digitalization.
Employee retention strategies in manufacturing industries
High turnover rates can significantly impact employee retention in the manufacturing industry, leading to increased hiring costs, decreased productivity, and operational disruptions. Implementing strong retention strategies can help businesses build a more committed and motivated workforce. Here are nine ideas for employee retention in the manufacturing industry:
1. Offer opportunities for growth
Manufacturing again has the image of having a lack of growth. And it’s understandable because it's hard to be engaged when you do the same repetitive tasks daily. To deal with it, manufacturing companies need to find out what their expectations are and work on how they can achieve those through training and experience. This will help employees be committed from day one, and over the long run, it builds loyalty, especially among a younger workforce.
To foster employee retention practices among tenured workers, companies invest in developing their skill sets because they know it will keep the boat afloat. It shows that the companies care for the careers of their employees and want them to climb up the ladder eventually within the company.
The best way they do this is by defining a clear career path for all employees from the moment they start working. They’re using skill management software, offering opportunities for professional development, and even encouraging managers to check in about the long-term goals of their teams.
2. Define expectations from the beginning
Research shows that broken commitments are one of the primary reasons for quitting. This is why setting realistic goals and expectations is necessary from the beginning. Companies are taking note of this as broken promises ruin employees' trust and confidence in the company. Instead, they’re being more transparent about the work opportunities and company culture.
Have a strong onboarding process where employees get a detailed insight into how the company functions, who their team members are, what the company policies are, work-life balance, safety precautions, and so on. The more exact your onboarding process is, the more realistic expectation standards you’re setting.
3. Re-evaluating the company's work environment
Creating a hazard-free and rather workable environment for employees in manufacturing is not too much to ask for. It becomes all the more important since loud noises, unconventional temperatures, dusty or oily materials, and the conditions can get frustrating quickly.
In such cases, companies are taking extra precautions to have cleaner and bigger breakrooms and add fans or heaters for proper air circulation where employees can take a breather. Similarly, if you’re not providing the necessities to work and survive daily in a manufacturing facility, your employees will likely leave and never look back.
Companies also re-evaluate the culture if needed. For example, do they encourage employees to take breaks? Do they provide free treats once in a while? Do they provide travel or insurance benefits? If companies are providing all the perks and showing that the employers care about their employees, the employees will give it a lot of thought before leaving.
4. Finding reasons for quitting
To retain, you first need to know why employees are quitting in the first place. To do so, companies are looking to develop retention strategies inside their firms rather than following a generic route from other industries to retain employees. The best way to do that is by directly asking your employees.
Companies are leveraging exit surveys as the most common and effective form of gathering employee feedback related to turnover. Other common methods are annual satisfaction surveys, exit interviews, and stay studies. Regardless of what you eventually use, these methods will give data-driven insights into why employees want to leave or even stay.
5. Employee engagement and recognition
Employees who are engaged in their workplace have exceedingly high quality of life and better performance at work than those who feel disengaged. Companies who take active efforts towards rewarding and recognizing employees have engaged workers whereas those who do not, may have ‘quite quitters’ - which is a major problem in the brewing.
The manufacturing industry today is termed ‘ The Great resignation’ era where more and more people are changing jobs and leaving their employers for better ones. Millions of people have now quit their jobs since the beginning of 2021 looking for jobs that are worthwhile. Some strategies that manufacturing companies should adopt are:
- Having a great workplace culture
- Positive growth culture
- Diversity and inclusiveness
- A well-rounded compensation
- Rewards and recognition programs
- Plenty of perks and benefits etc.,
These are all some tips to be devised carefully and effectively to ensure employee retention.
- Employers must be able to celebrate employee success and mark important achievements and milestones of employees to make them feel special and valued.
- Employee contributions should not be overlooked and recognition both in the formal and informal way must be carried out.
- Small to big rewards in the form of commissions and incentives, bonus, cash rewards, gift cards, tokens of appreciation, honor certificates and badges should all be incorporated in some ways.
An example of a great reward and recognition system that is being used in a manufacturing company is that of Trussway - a manufacturing company that utilized an employee reward program reflecting on employee wellness.
The company offers a plan that helps valuable employees to manage their retirement by putting in place a transition system to delay retirements, an effort to retain skilled employees.
Their suggestion and idea contest calls for great ideas from employees with a cash award of 1000 USD to 2500 USD for winners. They also have a safety-first approach towards employees that helps in cutting down on turnover.
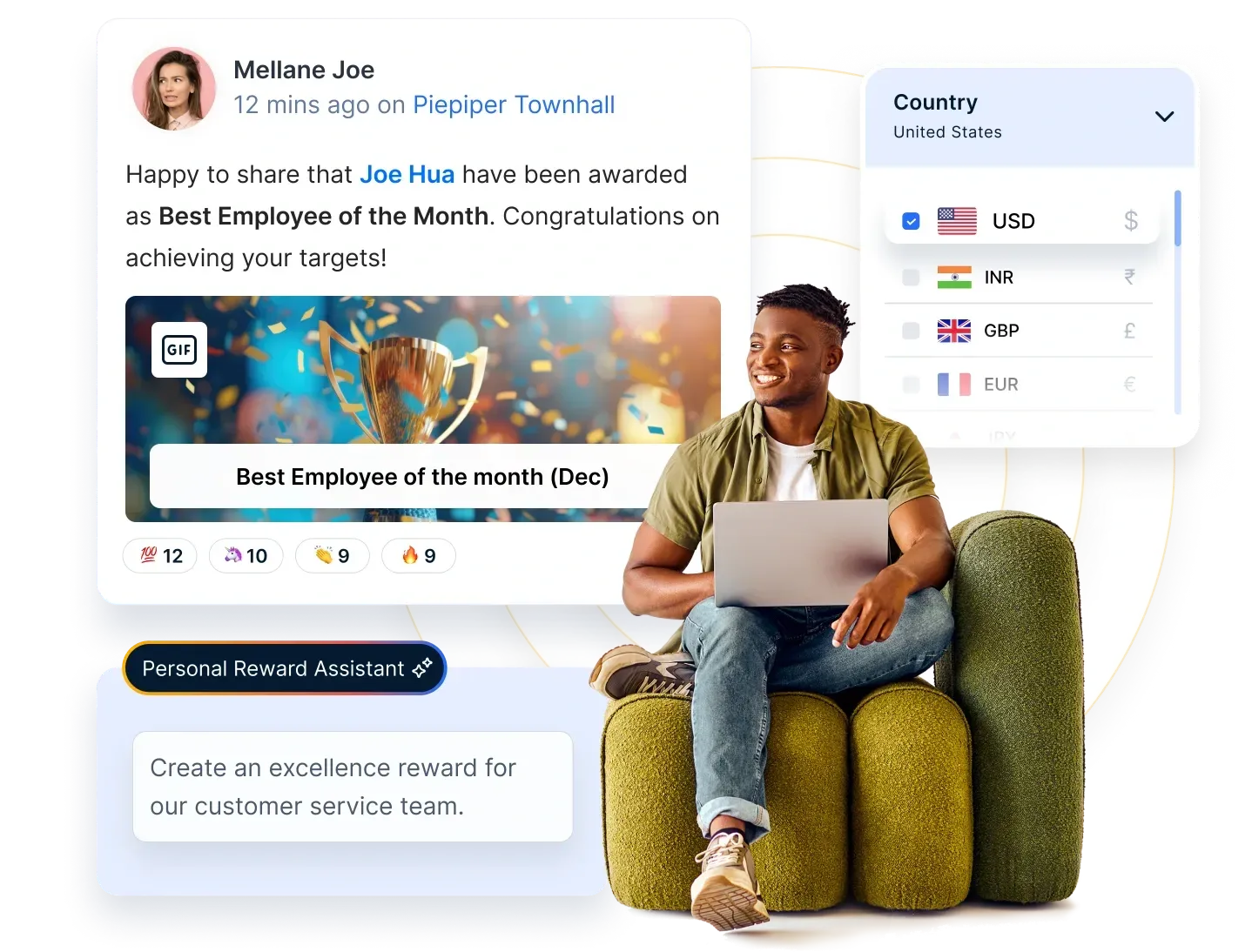
Reward Your Manufacturing Team the Right Way
Recognition isn’t just a perk—it’s the key to keeping employees engaged and committed. Show appreciation with milestone rewards, peer recognition, and performance-based incentives tailored for the manufacturing industry.
6. Competitive compensation and benefits
A study carried out by the manufacturing institute in collaboration with Colonial life revealed that finding the right skilled workforce has been a challenge for a long time and even with high demand in the market, 93 percent companies’ positions will remain unfulfilled due to competition in the manufacturing space.
83 percent of companies amongst these have increased their compensation to remain relevant and competitive in the market including benefits to employees, higher wages, perks and incentives to attract a skilled workforce.
The right compensation structure that both fits the budget bills of the company and improves job satisfaction, meets employee standards and expectations is a hard balance to strike.
By establishing a good compensation structure and clearly communicating the monetary and non monetary benefits of working with a given manufacturing facility, employee retention can be improved drastically.
Some strategies that manufacturing companies can make use of to provide good compensation and benefits to retain employees are:
- A well rounded compensation structure
Industry standard wages and a little extra can go a long way of showing how much one values their employees. Provide retirement, pension fund and other monetary benefits attached to wages as well for a well rounded compensation.
- Offer various benefits along with flexibility
Insurance benefits are becoming more and more sophisticated and therefore choosing attractive plans that cover employee aspects such as health, dental, vision, accidental benefit, family care and employee assistance programs.
- Monetary and non monetary benefits
Not all employees take monetary benefits as the only ones worth considering - there is a whole lot of non monetary benefits that makes employee lives easy in the manufacturing sector such as paid offs, paid vacations, opportunity for additional trainings and certified programs, flexible shifts and work hours, reward programs etc can all be a great way of compensating employees.
One of the best case studies of a company that has a well established compensation and benefit system and has retained manufacturing employees through it is Denso - an automotive parts manufacturing facility.
The company has come up with attractive compensation packages that focus more on retention of employees rather than attracting new employees.
They have put in place a 20 hour week shift to provide flexible hours which is most popular among employees. They also have other benefits such as free transport for employees, free meals, childcare facilities, education assistance for career development etc.
7. Training and skill development
Training and development are closely associated with employee turnover rates and attrition within organizations.
With career development and lack of training being the number 1 reason why employees left their jobs, providing opportunities to improve their skills, continue their education and investing in employee growth opportunities has become paramount. In a study, it was revealed that 74 percent of employees would be willing to retrain so as to remain employable and relevant in the industry.
In the manufacturing sector employees expect to be enrolled in continual training that help them with their jobs and with career development that can bring them closer to their goals in life.
Many companies in the world and especially in the US are providing growth opportunities by investing in the employees providing them with:
- Education opportunities
- Certified programs
- Workshops for skill development
- Online courses
- Completion of education and further education etc.
Companies are also expected to provide a clear career path and have career goal achievement meetings that help in establishing where the employee stands in their career goals.
Many companies and their HR teams are using a goal attainment meeting at 90 days of joining and annually to help employees in knowing where they are and where they can get to.
A solid case study of a company that utilizes this approach is Ketchie - a precision engineering manufacturing company. The company offers 4-day workweeks and a range of benefits to employees to retain them, one of the being the feedback system with focus on employee goals.
8. Safety and workplace environment
A ‘safety first’ approach towards employees shows that employees value them and care for their wellbeing. In a study, it was found that employees in the manufacturing industry had 300 work related fatalities each year and over 400,000 non fatal injuries were reported on average.
Safety in the workplace also is linked with compliance and factory audit requirements and therefore, manufacturing facilities must ensure that these guidelines are met so as to keep employees safe and retain them better.
Workplaces can have multiple hazards that are linked to serious harm and injury when not taken care of. Some example of employer responsibility towards safety of employees are:
- All water, fire and fall or injury prone areas should be clearly marked.
- Employees should be given protective gear, masks and PPE kits wherever applicable based on the type of facility.
- Employees should be given medical care, access to first aid and medical insurance to help them with any medical related emergencies.
- Large facilities should also have an in-house medical team.
- Regular audits must be conducted to ensure compliance to labor laws.
Safety at work is a key parameter for employee retention. 75 percent of employees in the US have reported that their workplace did not have the expected level of employee safety measures. 81 percent of employees believe that their physical safety is of utmost importance when choosing a workplace.
This means that employees who choose a company and stay with a company need to know that it is safe for them. Including medical care and medical insurance in the compensation is only scratching the surface of what employees expect from companies.
- Ensuring a safe and healthy workplace
- Addressing workplace hazards and concerns
- The correlation between safety and employee retention
9. Data-driven retention strategies
Employers can utilize trustworthy and predictive data to check on employee turnover and retention rates so that companies can identify the areas where they need to work on potential risk factors that are causing them the churn.
Losing out on trained and skilled employees can cost 13 to 23 percent of annual compensation apart from other risk factors such as losing out on stakeholders, accounts they dealt with and clients they handled.
Using data drive strategies and predictive models, HR teams can analyze what causes employees to leave and come up with risk mitigation programs. Some facts and strategies of data drive retention approach are:
Many major companies are now using various softwares and tools to record employee behavior, mood, engagement levels, stress levels, workload, peer relationships etc to analyze their retention tendency.
Data collection and research organizations such as Gartner have been helping companies collect data in the most unconventional ways to analyze employee behavior and the turnover of employees in the manufacturing sector.
Use of exit interviews is critical to understand what causes employees to leave and use the feedback and data to help create better and effective retention strategies
Using the right selection model such as data driven recruitment helps in retaining employees as most people quit because they find that their jobs do not cater to their long term goals.
Glassdoor research suggests that most people start looking for jobs in January which can help employers to place special employee attention to help mitigate attrition risk.
Use of stay interviews and an associated retention/ stay bonus and a regular method of employee engagement survey can help in increasing employee retention.
An example of a company that uses data driven employee retention using predictive analytics is Continental - an automotive parts manufacturer. The company's Mexico factory had a very high turnover forcing the use of predictive analysis and data driven models to understand how to hire the right employees, predicting employee turnover and mitigating risk through various strategies including action plans, surveys, follow ups, diversity and inclusion etc.
Examples of companies in the manufacturing industry that are doing an awesome job in attracting & engaging employees
Here are the examples of companies in the manufacturing industry that are doing an awesome job in attracting & engaging employees.
1. NVIDIA
Nvidia is known in the graphic processing units and computer chips industry. The company is considered a benchmark for encouraging employee engagement in the manufacturing sector.
It regularly conducts activities such as community outreach and team-building events to promote better working relationships and eliminate unhealthy competition. It also fosters a productive environment so workers can hone their creative skills with adequate autonomy.
2. Stryker
The leading medical technology company is known to attract existing employees for new roles and provide opportunities in research and development, product management, and quality assurance. It also engages its employees with amazing benefits such as comprehensive health coverage, tuition assistance, and a retirement savings plan.
3. Apple
Apple has created an innovation-oriented culture where it has transformed its units to better its human capital and promote team development. It builds engagement by making employees its biggest brand ambassadors and providing them with product benefits and discounts. It also offers free stock shares and grants to encourage them and enhance their creativity in the workplace.
4. General Electric
General Electric has brought about many changes in its recruitment processes and has focused on creating a balanced recruitment strategy that encourages more women to apply.
In one of its promotional videos, it announced GE’s goal of employing more than 20,000 women in technical roles by 2020. It also places a lot of focus on employee engagement and development by providing tuition reimbursement and extensive training for employees to grow in their careers.
5. L’oreal
L’oreal created an employee value proposition filled by its current employees to attract new ones. The employee value proposition includes the values and culture that the company embodies and provides for its employees.
The current employees concluded that L’oreal is an inspiring company, a school of excellence and working there is a thrilling experience. The result of this? Almost 70% of their LinkedIn followers want to apply for the company.
Retain your manufacturing workforce & reduce turnover with Empuls
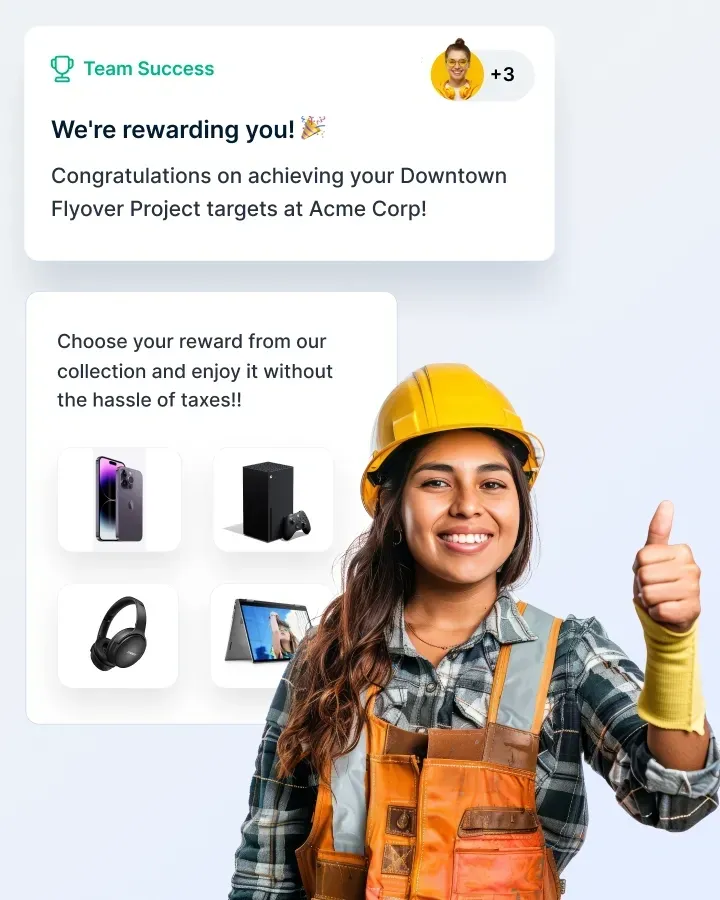
High turnover is a constant challenge in the manufacturing industry. Long shifts, physically demanding work, and lack of recognition often leave employees feeling undervalued and disconnected. Replacing skilled workers is costly, but the real challenge lies in keeping them engaged, motivated, and committed to your organization.
Empuls provides employee engagement solutions for manufacturing that go beyond just paychecks—creating a workplace where employees feel appreciated, heard, and invested in the company’s success.
How Empuls helps retain manufacturing employees:
- Recognize & reward loyalty: Celebrate work anniversaries, safety achievements, and outstanding contributions with meaningful rewards and incentives.
- Give employees a voice: Conduct real-time pulse surveys to understand concerns, address challenges, and foster a culture of continuous improvement.
- Strengthen workplace connection: Keep frontline and factory workers engaged through a social intranet that fosters communication and teamwork.
- Provide meaningful perks & benefits: Offer tax-free fringe benefits, milestone rewards, and incentives that add real value to employees' lives.
- Boost job satisfaction & motivation: Create an environment where employees feel respected, supported, and motivated to stay for the long term.
Retention isn’t just about filling positions—it’s about creating an environment where employees want to stay. With Empuls, manufacturing companies can build a workplace culture that prioritizes recognition, engagement, and long-term commitment. Connect with our employee engagement experts now!
Finishing thoughts
Like most industries, employees are also the biggest asset in the manufacturing industry. But today’s workforce has a lot of options at their disposal. They have access to resources and connections that can help them land a good job in any other field.
As a result, manufacturing companies are making special efforts to attract and retain these employees as manufacturing work environments often lead to high turnovers, which you can take as an example.