How to Calculate Variable Cost: A Simple Guide for Smarter Business Budgeting
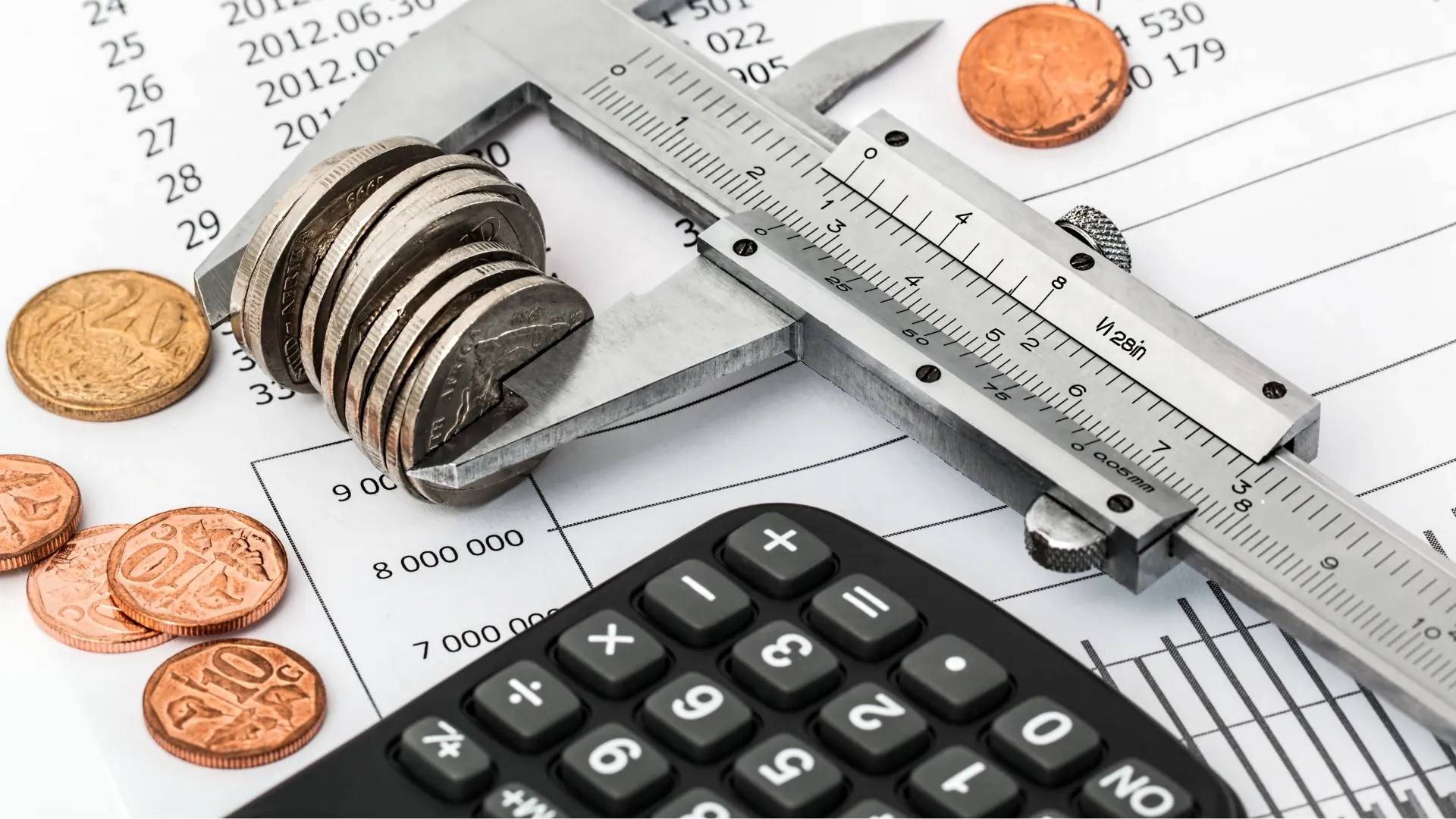
If you are someone who owns a business or if you are thinking of starting a business, chances are, you have come across the term Variable Cost. Many different kinds of costs are associated with business and perhaps the most crucial of them all is the variable cost.
The variable cost helps businesses to set the price for their products or services and help in overall budgeting for their production process.
In finance and accounting, variable cost is defined as the type of cost that changes with the production, sales and gross revenue. It is a recurring cost to the company and rises and falls based on how much goods or services are produced or provided.
Companies who have high variable costs are more likely to have lower profit margins but they are also companies that can achieve the breaking point very easily. We will go into the details of variable costs, the examples of variable costs and calculating variable costs for your business with examples.
What are variable costs?
In finance and accounting, variable costs are expenses that change in direct proportion to a company’s production or sales volume. These recurring costs rise as output increases and fall when production slows down.
Companies with high variable costs may have lower profit margins but often reach their break-even point faster. Understanding variable costs helps businesses optimize pricing strategies and streamline budgeting during the production process.
Examples of variable costs
There are many different kinds of variable costs in a company or a production facility.
Some of the common examples of variable costs are:
1. Labor
Labor is the number one variable cost. Labor is also referred to as piece rate labor as it is the wage that is paid out to laborers based on their output as compensation for their work. Most kinds of production and manufacturing facilities incur labor charges that need to be paid out daily/weekly and this cost is variable as it rises when there is a higher number of hours/units produced and lower when there is less.
2. Raw materials
Raw material is another major cost and is associated with the amount of production that has been planned. As a typical variable cost, raw material costs increase when there is a planned higher production level and lower when the company has to produce fewer. Raw materials or direct material cost is the cost associated with the purchase of material that goes into making the products.
3. Shipping costs
Shipping costs or cost of freight is the cost that a company needs to pay to transport the materials to the production facility and the manufactured goods from the production to the distribution or godown.
This cost also increases or decreases with the number of goods that is taken to and fro and therefore varies with the production level.
Other examples of variable costs include:
- Credit card fees for the company upon usage of credit cards (mostly in service industry)
- Commissions such as overtime, sales commission etc in a production/retail facility
- Packaging cost is a variable cost in production facilities
How to calculate variable costs?
The formula for calculating variable cost is:
It is important for businesses to calculate and familiarize with their variable costs as it helps them in budgeting for funds while in the production stage and also helps them to fix the retail price of the product.
By analyzing how much is spent on producing the product, a manufacturer can set the price for retail so that the company can break even and make profits on the sale of these goods.
A simple formula to calculate the variable cost is to write down all the costs you incur for one unit produced and multiply this by the total number of units produced.
Those who want to use variable costs to determine the overall cost of the product can use the following two approaches:
1. Direct cost method
The direct cost method calculates all the direct variable costs that go into producing a unit or the total units and does not consider any fixed costs such as rent, salaries, machinery or depreciation.
In this method direct costs of producing a product such as direct materials, direct labor, unit packaging charges, per unit freight charges etc are taken into account while calculating the cost.
-> Direct materials - 2 USD
-> Direct Labor - 1.5 USD
-> Packaging charges - 0.25 USD
-> Freight - 0.25 USD
-> Total variable Cost being 4 USD, the manufacturer should exceed this value as it is the minimum cost to make the product.
2. Contribution margin method
The contribution margin method is used to calculate the profitability of the product or service by deducting the total variable costs from the total sales revenue. This method helps in understanding how much profit can be earned by selling a product and helps determine the unit's price.
To improve the profitability, the company must either have a high selling price or low variable cost.
For example: The total variable cost including material (2 USD), labor (1.5 USD), shipping and packaging (0.5 USD) is 4 USD.
For 1000 units sold, the total variable cost is 4000 USD. If the total sales revenue is 10,000 USD, then contribution margin is calculated as:
10,000-4000 USD = 6000 USD.
Best practices for managing variable costs
Managing variable costs helps in many important decisions such as setting the product's sales price, analyzing the cost expenditure and therefore reducing overheads, planning a production budget etc.
Businesses must strive to manage their variable costs so that they can have higher profitability.
Here are some best practices for managing variable costs:
1. Lower material costs
Buying in bulk and at discounted wholesale prices can help in lowering the material costs. Low material cost helps in keeping the unit costs less but it can be sold at a nominal sales price, improving the profitability.
2. Economies of scale
It is a common practice that producing higher in volume helps in cutting down the overall variable costs and therefore companies try to go in for larger volumes to achieve economies of scale.
3. Lower labor cost
Reducing your overall labor expenses is important as labor costs add up and can significantly increase your variable cost. Investing in automated machinery can help bring down variable cost in the long run.
These are some of the best industry practices that can help decrease the variable cost so that you can keep your product manufacturing costs low and thus improve net profit.
While managing variable costs like labor, materials, and shipping is essential, there's another powerful lever often overlooked—employee engagement. That’s where Empuls steps in.
1. Reduce high labor-related variable costs
Challenge: Labor is one of the biggest variable costs. High turnover, absenteeism, and disengagement inflate labor expenses and hurt productivity.
Empuls solution:
- Boost retention with AI-powered recognition & rewards, service awards, and career milestone celebrations.
- Reduce absenteeism and increase morale through pulse surveys and data-driven engagement strategies.
- Provide early access to earned wages, reducing stress and absenteeism from financial emergencies.
2. Improve efficiency to achieve economies of scale
Challenge: Companies often need to scale output to reduce per-unit variable costs, but disengaged teams are less productive.
Empuls solution:
- Drive high-performing teams with continuous feedback loops and AI nudges for managers to act on insights.
- Use goal alignment tools and community platforms to foster accountability and focus.
3. Drive value without increasing variable overheads
Challenge: Incentive and perk programs can become costly if not managed well.
Empuls solution:
- Use bill-on-redemption rewards—pay only when employees redeem, avoiding unnecessary variable spending.
- Offer stackable savings through perks & discounts that feel like a pay hike without increasing payroll.
Empuls isn't just a “nice-to-have” for HR—it’s a strategic tool for reducing avoidable variable costs, increasing workforce ROI, and scaling productivity without proportional cost increases.
Conclusion
Variable costs are a fundamental part of running any business, especially in manufacturing and service industries. By understanding how they work and implementing best practices to manage them, businesses can improve pricing strategies, control production budgets, and maximize profits.
Start by identifying your variable costs, use the right calculation methods, and continuously look for ways to optimize. Smart management of variable costs is a key driver of sustainable growth.